Residue FCC
Maximize Residual Fuel Oil Conversion
American Petroleum US and American Petroleum Pvt, Ltd process utilizes an effective two-stage stacked regenerator with catalyst cooler(s) to provide you with a cost-effective means for converting moderate to severely contaminated feed-stocks to gasoline and lighter components. These features together with other important design considerations manage the high heat of combustion, metals lay-down on circulating catalyst, and other challenges associated with the processing of reduced crude.
- The two-stage regeneration process is highly efficient at moderating regeneration temperatures necessary to minimize catalyst damage while maintaining sufficient removal of carbon on catalyst to ensure maximum conversion of residual feed within the reactor. The catalyst cooler(s) provide the primary means of heat removal for the process and provide an added unit flexibility relative to conventional designs.
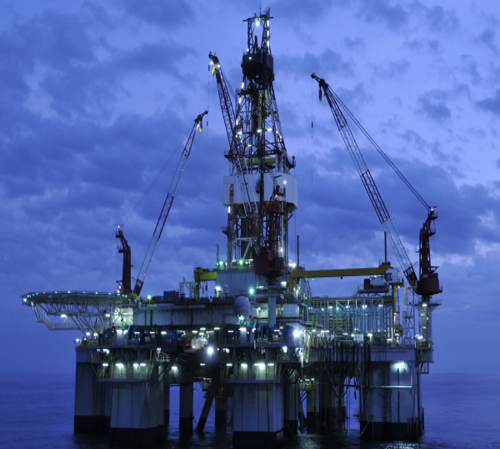
- High selectivity to gasoline and other high-value products is achieved by optimized feedstock/catalyst mixing, effective post-riser catalyst/oil disengagement, metals passivation, and other design and operating techniques.
- With these unique design features, American Petroleum US and American Petroleum Pvt, Ltd Process allows the greatest flexibility in feedstock quality (Conradson carbon and metals) while achieving high conversion and maximum selectivity to valuable products, maximizing your margins and overall project ROI.
Benefits to the FCC operator are:
- Improved unit reliability, on-stream factor
- Minimize lost production and overall refinery impact
- Avoid equipment damage